The Internet of Things in Manufacturing: How IoT Is Changing Manufacturing
The Internet of Things and connected devices are becoming commonplace in households and the workplace. The overall number of IoT devices has already exceeded 26 billion—the most popular ones being thermostats and locks for smart homes, fitness trackers, and personal assistants.
It’s no wonder that the Internet of Things is also widely used in manufacturing. When the industry struggled to adapt to the changing economic landscape and rebuild slow linear supply chains, the IoT provided companies with the tools needed to modernize the field.
The set of applications provided by the industrial IoT is extensive—the technology can increase workplace safety, fight talent shortage, and increase the quality of the end product.
In this blog post, we’ll examine the state of the Internet of Things in manufacturing, go over its most promising applications, and examine the benefits of IoT solution for supply chain.
Manufacturing industry frontrunners have already started to implement IoT into production and the supply chain. While some companies are yet exploring the market and mapping out pilot projects to stay up on trends, others are ready to roll out full-fledged digital solutions.
The industrial IoT market is rapidly developing as manufacturers come to terms with digitization and automation. According to a report issued by PwC, 90% of manufacturers believe that digitizing the production process will bring more long-term benefits than risks.
IoT is among the main driving forces of digital transformation in manufacturing. According to Zion Research, the Industrial IoT (IIoT) market value is expected to reach $232 billion dollars by 2023. The technology is expected to improve data gathering, employee safety, and operational efficiency. According to Accenture, 46% of respondents among American companies see the Internet of Things as an opportunity to increase employees productivity.
As it will only be possible to fully assess the performance of most industrial IoT-based innovations, in the long run, the next decade will be decisive for Industry 4.0. As for now, it’s clear that IoT is a lucrative market for manufacturers worth exploring and investing in.
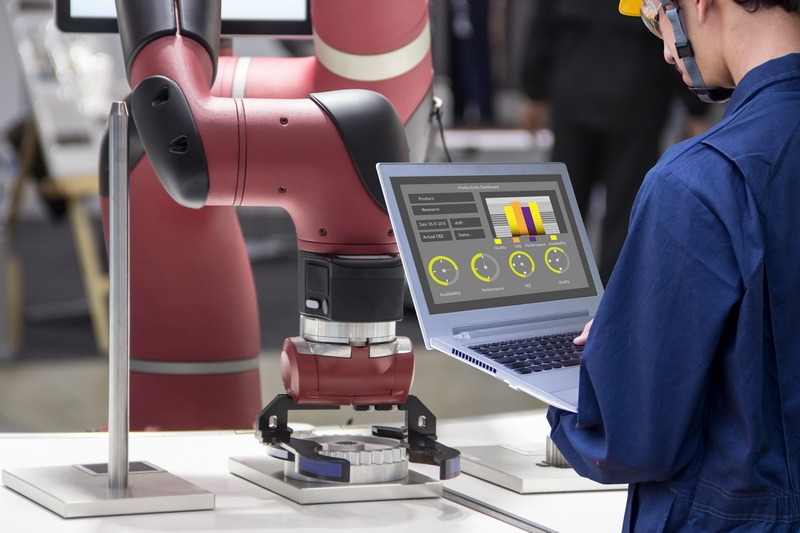
Smart manufacturing IoT is empowering dozens of devices that are essential for manufacturing companies — sensors, industrial robots, cameras, and smart meter systems, as well as distributed control solutions. As a result, the technology finds its applications in all areas of production and supply.
The following objectives can be reached thanks to the industrial IoT:
- Real-time monitoring. The Internet of Things allows everybody involved in the process to keep updated on the production flow increasing the speed and efficiency of communication and the overall manufacturing pace. Using real-time monitoring applications for manufacturing, companies will be able to reduce the amount of work that’s normally performed during the production cycle and eliminate waste.
- Remote equipment management. Thanks to connected sensors, a manager will be able to oversee the state of equipment without having to visit the site. This will improve the productivity of employees, create proper storage conditions for manufacturing tools, and reduce costs.
- Condition-based downtime alerts to reduce machine downtime. While traditional maintenance is time- and effort-consuming, it often fails to provide manufacturers with clear insights regarding plant performance and the shortcomings of the production flow. Random inspections, walk-throughs, and once-a-year shutdowns provide a selective understanding of the process, not the bigger picture. With the Internet of Things, a manufacturer can implement condition-based management system, a proactive site management approach. By receiving IoT-based downtime alerts, you’ll be able to improve throughput and reduce machine downtime.
- Identifying and correcting quality issues by aggregating product, customer, and third-party data. This way, you’ll be able to react to defects faster and fix them before the product is brought to market.
- Reducing shared costs in the value chain by providing cross-channel visibility into inventories. Back in 2015, Gartner remarked businesses in the US and Europe were not happy with the lack of ways to effectively fulfill multi-channel orders as they had little insight into inventories. Using IoT in warehouse management and logistics, all parties involved in the supply chain will be able to access the real-time inventory status — this enables optimizing the value chain and reducing its costs.
- Enabling a manager to see the real-time status of the product line. The Internet of Things allows the supply manager to track the delivery and distribution of a product line step-by-step.
- Tracking product deterioration and gathering customer insight. IoT is capable of tracking usage patterns — this way, a manufacturer will be able to understand which features of the product are popular and which, on the contrary, should be removed. As soon as the drop in demand is spotted, the company will be able to engineer the product before the brand’s reputation starts taking a hit.
- Using predictive maintenance to minimize equipment failure and service cost. Manufacturers deploy IoT to avoid bottlenecks during the production process, avoid overloads that could lead to equipment deterioration, and replace broken machines without causing chaos on site.
1. Digital factories
The Internet of Things provides an opportunity to establish a connection between the company, the manufacturers of the equipment it uses for production, employees involved in product design and development, and supply chain managers. Such a connected factory is cheaper to maintain and faster to manage.
The digital connection between all the areas of the plant will allow managers to track employee performance, the efficiency of equipment installed, and the feedback from end users. The use of IoT makes sharing crucial data between team members easier and 100%-paperless.
2. Facility management
IoT and smart manufacturing devices improve the speed and quality of facility maintenance. Sometimes, managers have to oversee temperature- or vibration-sensitive equipment that’s sensitive to slightest environmental changes.
Predicting the deviation from optimal functionality parameters without the help of advanced technology is practically impossible. IoT sensors, on the other hand, are capable of alerting a facility manager as soon as there are any changes that could put manufacturing tools in jeopardy.
By controlling the working environment with facility management solutions, you’ll be able to reduce maintenance costs, increase operational efficiency, and reduce the downtime.
3. Inventory management
Thanks to the Internet of Things, factory managers will be able to trace all the materials needed for manufacturing on the item-level. This way, one can renew the inventory without having to put the production process on hold.
Inventory planning would be improved as well as soon as the Internet of Things is implemented as you will be able to predict how much time it takes for a certain amount of resources to run out and increase the precision of long-term planning.
4. Plant security management
IoT manufacturing impact on workplace safety and the security of the site itself. Health trackers will alert managers as soon as an employee is at risk of injury or health damage.
With the technology, you’ll be able to keep track of the overall number of injuries and health-related incidents during the manufacturing process, find out what caused such situations, and come up with ways to predict similar events in the future.
IoT is a powerful tool for theft protection as it can notify a manager in case of any equipment and property damage, keep logs of the time when a certain machine was broken, lost, or stolen.
5. Quality control
The Internet of Things can control product development on each stage, tracking the quality of materials, temperature and the manufacturing environment, the amount of waste created per product, and so on. The plant manager will be getting detailed reports regarding each step of product design, transportation, and distribution of ready goods.
All this data allows managers to implement in-depth quality control, improve the workflow, the environment, the quality of equipment, or vehicles used for transportation.
6. Supply chain optimization
Devices with IoT help manufacturing companies track products as they move through the supply chain and integrate it into PLM, ERP, or another system the company uses for reporting and data storage. In case a supply chain deviates from the plan, a manufacturer will be able to trace back to the cause of a delay as all the interdependencies were tracked.
7. Packaging optimization
IoT collects usage patterns and reports on how a product is normally used by customers. Thus, production managers will be able to rework the packaging, reduce its costs, or change a design in a way that would be resonating with the end customer on a deeper level.
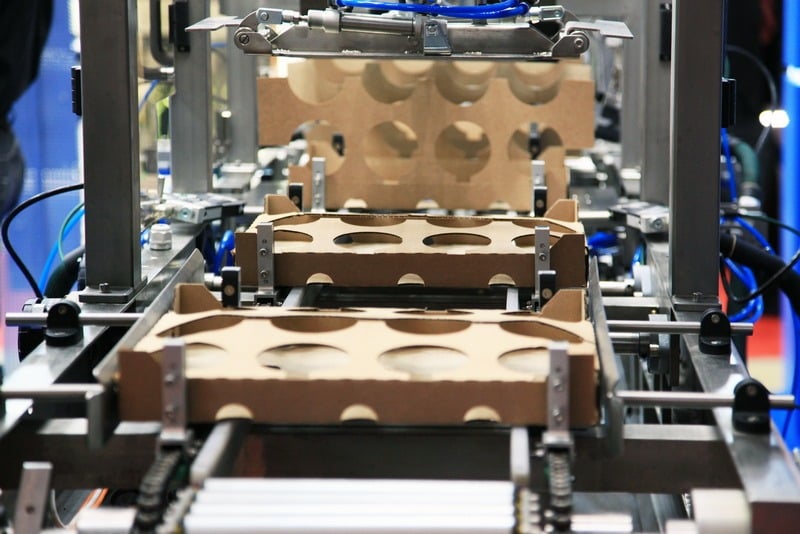
Replacing dated insights with the real-time ones is a key IoT change manufacturing companies can benefit from. In areas like employee health or equipment maintenance, it’s crucial to get updates as soon as possible. Before, it would’ve been impossible — now, the tables have turned.
Timely insights are not the only benefits of IoT. Here are other advantages of technology for factory managers and employees.
1. Improves employee productivity and safety
Workplace safety is a common problem for manufacturing companies — it’s so widespread that over 2 million people die from work-related diseases each year in the US alone. The Internet of Things is among the few tools capable of resolving the issue on a relatively limited budget.
By monitoring alone, IoT can reduce the number of accidents at work. The technology can track:
- Environmental properties to ensure dangerous chemicals are not released in the air;
- The quality of the equipment;
- Employee well-being.
As soon as there are signs of environmental distress or evidence of health-related issues, a company’s management will be able to use preventive measures to prevent tragic accidents from happening.
2. Improves the efficiency of inventory maintenance
Filling in spreadsheets manually in order to keep track of inventory logs can lead to errors and eventually jeopardize the manufacturing process as a whole. Paired with RFID tags, the Internet of Things can eliminate human error and automatically share inventory data with management systems. You will also be able to share the inventory data with dedicated departments.
Thanks to IoT, keeping track of lost items or the lack of materials becomes easier. You’ll be able to ensure your tax returns and reports are precise as well.
3. Increased quality control
The ignorance of product quality can have long-lasting effects for a company’s reputation and cut the user base tremendously. Thanks to the Internet of Things, the high standards of the manufacturing process will be maintained at each stage. The technology is capable of pinpointing faulty equipment so that a site manager can settle the issue with the manufacturer of the machine, the changes in the environment, the lack of employee productivity, or an issue during transportation.
4. Reduced downtime
IoT can prevent situations when a machine stops working in the middle of the cycle. Such incidents are highly wasteful both in terms of time and resources. Thanks to IoT sensors, you’ll be able to reduce the machine downtime allowing for no missed opportunities or spoiled materials and equipment.
5. Informed decision-making
A possibility to predict the challenges a manager has to face during the manufacturing cycle allows companies to switch the management paradigm from reactive (replacing broken equipment with the new one, dealing with issues as they pile up) to proactive (reducing the load on equipment before it gets defective, learning the duration of each manufacturing cycle, and increasing transparency across departments).
6. Energy spending control
As most managers keep track of energy spending from monthly bills, it’s almost impossible to break it down and understand how much energy each device consumes over a selected period of time. IoT power monitor and management systems provide manufacturing companies with granular insights on energy consumption for all devices involved in the production. You’ll be able to decide on all the ways to optimize the use of equipment and reduce power waste.
The Internet of Things is capable of not just providing manufacturers with real-time data scanned by sensors but predicting maintenance needs as well. By analyzing large volumes of all gathered data, the technology is capable of detecting early signs of equipment failure, concerning environmental changes, and other factors crucial for manufacturing.
Out of all the applications of predictive analytics, the main ones are:
- Predicting and preventing hardware failures;
- Improving safety within the workplace;
- Streamlining and optimizing the workflow.
In order to build a system with IoT predictive maintenance in manufacturing, IoT software development agency puts together the following elements:
- Industrial equipment with sensors for data gathering;
- Field gateways for data filtering and reprocessing;
- Streaming data processor that allows continuous data flow and transmission to a data lake;
- A data lake to store the data gathered earlier by sensors;
- A big data warehouse that stores data that has already been sorted.
Conclusion
There’s hardly an industry more equipped to showcase the full potential of the Internet of Things than manufacturing. Companies can use IoT sensors to rebuild old-fashioned processes from scratch, monitor the equipment quality and the productivity of employees, manage supply chains remotely, and predict potential challenges long before they arise.
If you are implementing IoT solutions for manufacturing and looking for skilled IoT software developers, contact our team. In our portfolio, you’ll find a range of IoT and big data projects and learn how we have helped companies across various industries optimize their business processes.
To discuss a project, leave us a message. We look forward to hearing from you.