Top 5 Practical Warehouse Optimization Strategies and Techniques, No AI or Robots Required
The buzz around warehouse optimization with drones, AI, and robots is everywhere. But for many, the question is: so what?
Trust us: if you’re still relying on paper documents, Excel sheets, or legacy software in your warehouse operations, you’re not alone. A recent survey by PackageX found that:
- 40% of warehouses use outdated methods like pen and paper.
- 55% rely on legacy systems that aren’t built for modern needs.
- Only 5% have adopted advanced automation.
According to Farrukh Mahboob, CEO of PackageX, “80% of warehouses lack even basic automation.”
So, while high-tech solutions grab headlines, the majority of warehouses aren’t ready for robots yet. The first step is to optimize a warehouse and automate everyday processes, and then build up to bigger improvements.
At Digiteum, we’ll show you how to optimize a warehouse with custom logistics software development.
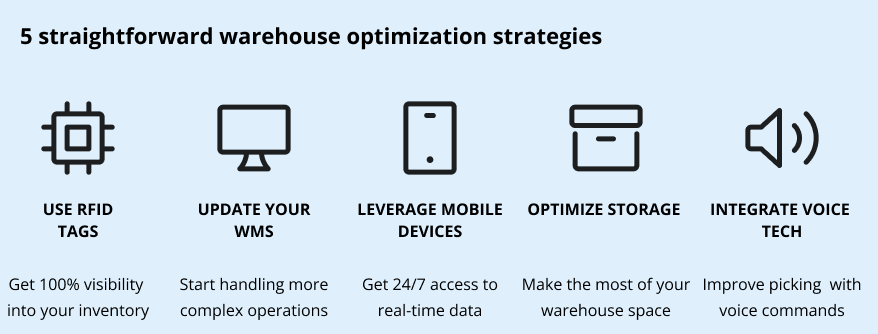
As retail evolves, traditional SKUs like “Red T-Shirt, Size M” or “Organic Almond Milk, 1 Liter” are becoming outdated. They’re too broad and often cause errors. For example, if the system can’t tell the difference between two brands of almond milk, it could lead to overstocking one brand and understocking the other. This results in inventory problems and unhappy customers.
That’s where item-level tracking comes in. It uses Electronic Product Codes (EPCs) and RFID technology to monitor each unique item throughout the supply chain. This means you can track hundreds of items at once without needing a direct line of sight.
This approach dramatically boosts inventory accuracy – from about 65% to over 95%, according to Auburn University’s RFID Lab. With higher accuracy, you’ll experience fewer stockouts, better inventory management, and increased sales.
As Bill Hardgrave of the RFID Lab notes, “RFID increases inventory accuracy to more than 95%, but only if retailers use the data to improve operations.”
Real-life example: Decathlon gets 100% visibility into its inventory
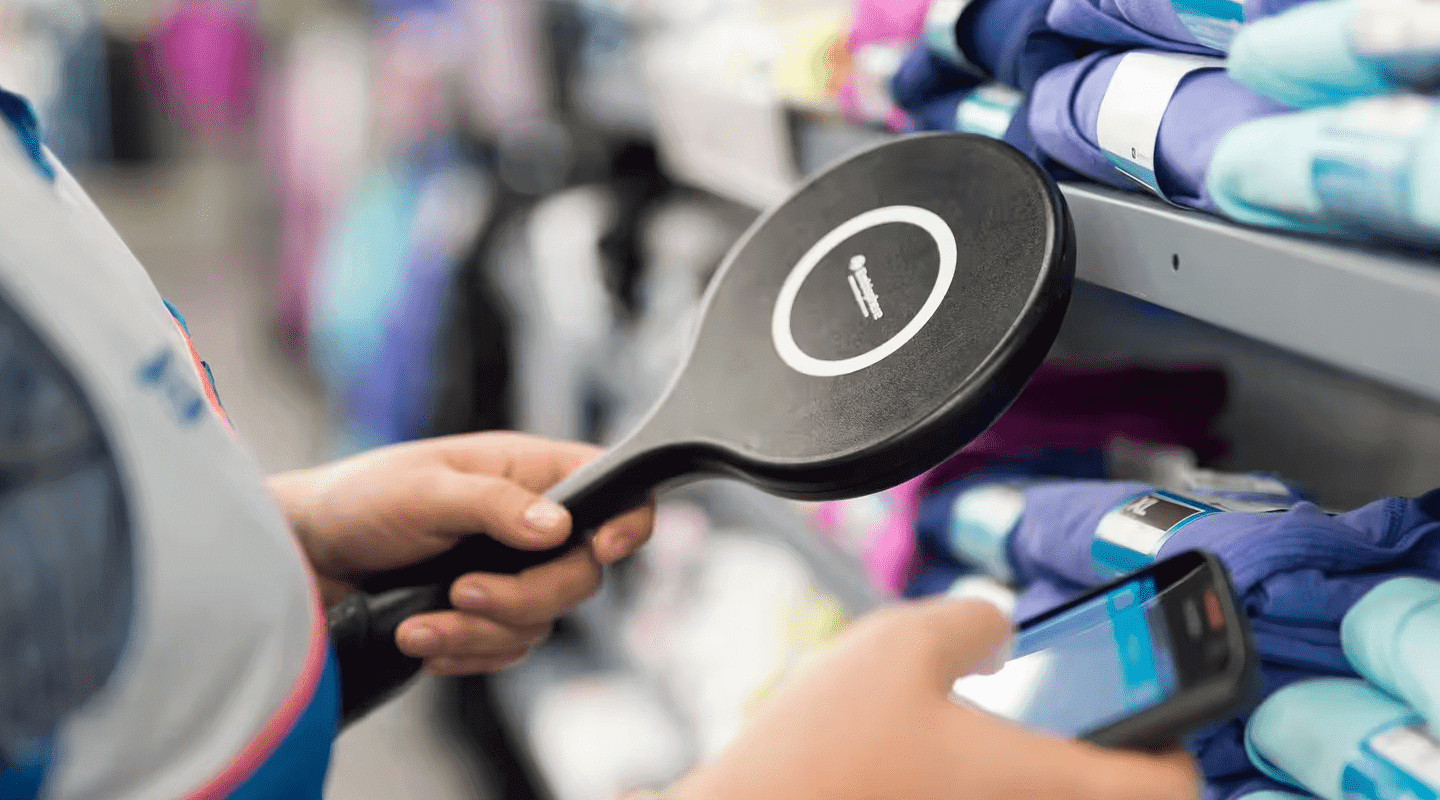
Image credit: Decathlon
Decathlon adopted RFID technology as one of its key warehouse optimization techniques. Each product is tagged with a unique RFID code, and over 50,000 RFID readers are used in their warehouses, distribution centers, and stores.
This setup lets Decathlon track products in real time and manage inventory accurately. The technology monitors each item from the factory to the store. This simplifies operations and improves supply chain efficiency.
The move to RFID provides Decathlon with better inventory control and streamlines logistics for its global network.
Benefits
- Real-time inventory tracking. RFID provides instant updates on product locations and quantities.
- Quick operations. Automated processes with RFID speed up operations and minimize manual tasks.
- Full product visibility. RFID helps quickly find products and check their availability, providing better customer service and fewer stockouts.
A Warehouse Management System (WMS) is essential for optimizing warehouse operations, including inventory receiving, put-away, picking, shipping, and replenishment.
However, many warehouses face issues with legacy or homegrown WMS. Common problems include:
- Integration issues. The WMS may not integrate well with other critical business systems. This lack of integration can disrupt workflow and data sharing.
- Inadequate functionality. The system might struggle with specific industry requirements or advanced functionalities. This includes handling complex inventory management or performing advanced analytics.
- Limited flexibility and scalability. If the WMS isn’t flexible or scalable enough, it could struggle to keep up as your business grows or changes.
These issues can be addressed with a WMS upgrade. Options for upgrading include:
- Enhancing the core WMS with additional functionality, for example, any of the 4 types of data analytics.
- Adding new custom modules and third-party warehouse optimization solutions to the existing system.
- Improving data synchronization with other business systems, such as ERP or CRM.
- Migrating to a new WMS.
Maximize your WMS with Digiteum
Digiteum brings extensive experience in tech implementations and upgrades, including WMS and ERP. Our dedicated team will work closely with you to ensure a smooth and effective process.
Contact expertsReal-life example: A major furniture retailer boosts warehouse efficiency with a new WMS
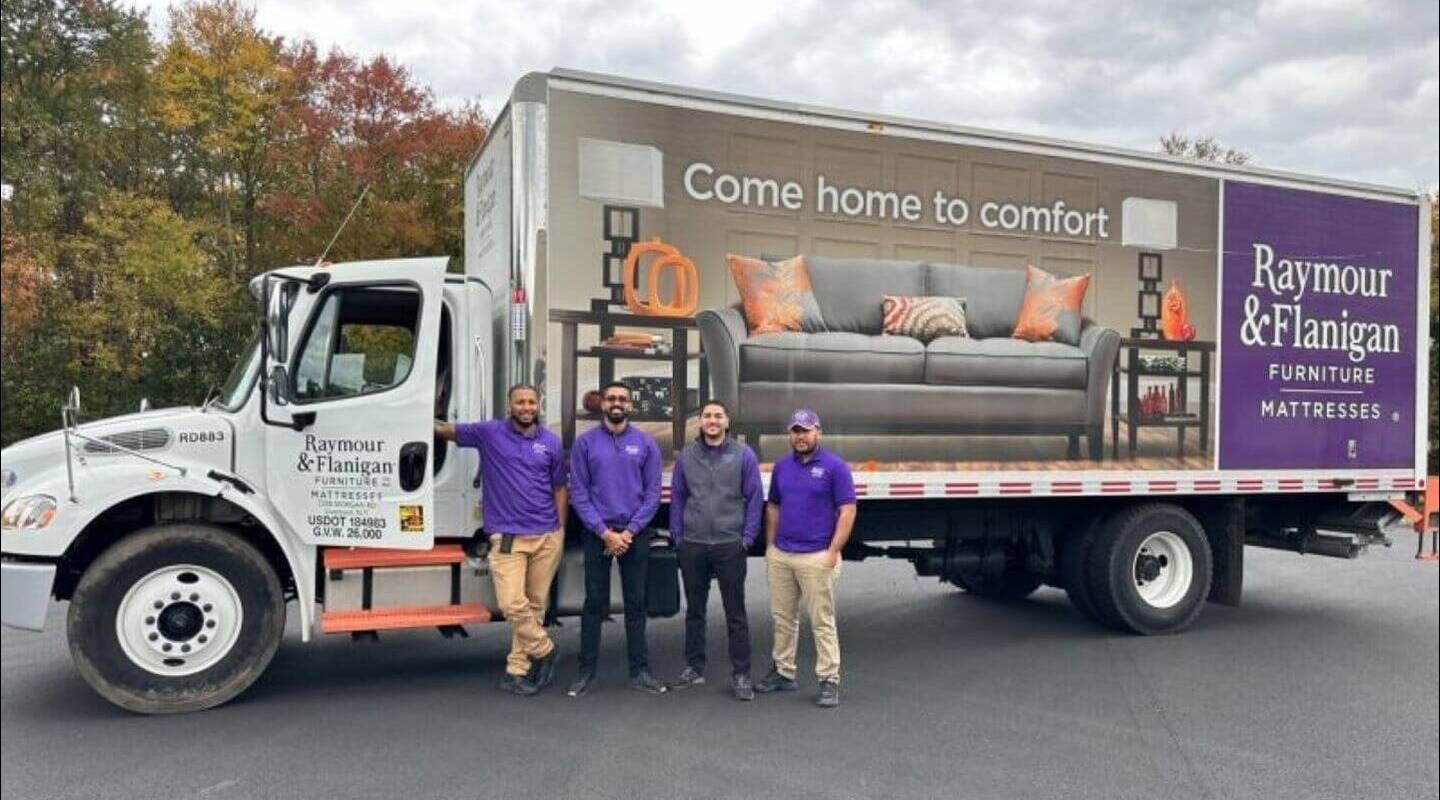
Image credit: Great Place To Work®
Raymour & Flanigan, the largest furniture retailer in the Northeast, was struggling with its outdated WMS. The system didn’t integrate well with other business software and lacked advanced features. As a result, warehouse operations were inefficient, relying heavily on staff’s “tribal knowledge” and old-school practices.
To fix this, they decided to upgrade both their WMS and ERP systems. They went with Körber’s WMS and NetSuite ERP, ensuring a smooth integration with help from their tech partner.
They started the rollout at a simpler distribution center and are now expanding to over 20 locations. The company expects to see a return on investment within 24 months.
Benefits
- Increased efficiency. WMS upgrades make warehouse operations smoother and faster. Picking and loading become easier, and handling inbound shipments is more efficient.
- Warehouse storage optimization. With more advanced systems, warehouses can learn how to optimize warehouse space. This means more storage capacity and better inventory management.
- Lower costs and quick training. More advanced WMS systems help cut expenses and get staff up to speed quickly.
Without real-time data, managing a warehouse feels like trying to run operations blindfolded – delays pile up, issues slip through the cracks, and frustration grows.
That’s where mobile technology steps in. It provides visibility, one of the main benefits of warehouse automation. By putting real-time data in managers’ hands, they can monitor inventory, track product movement, and adjust on the fly, all without being stuck at a desk.
Mobile devices, paired with advanced data collection tools and performance software, give you the end-to-end visibility needed to make quick, informed decisions. Plus, integrating with ERP and WMS systems ensures the entire supply chain runs smoothly, keeping everything on track and efficient.
Real-life example: A service provider automates warehouse inventory processes
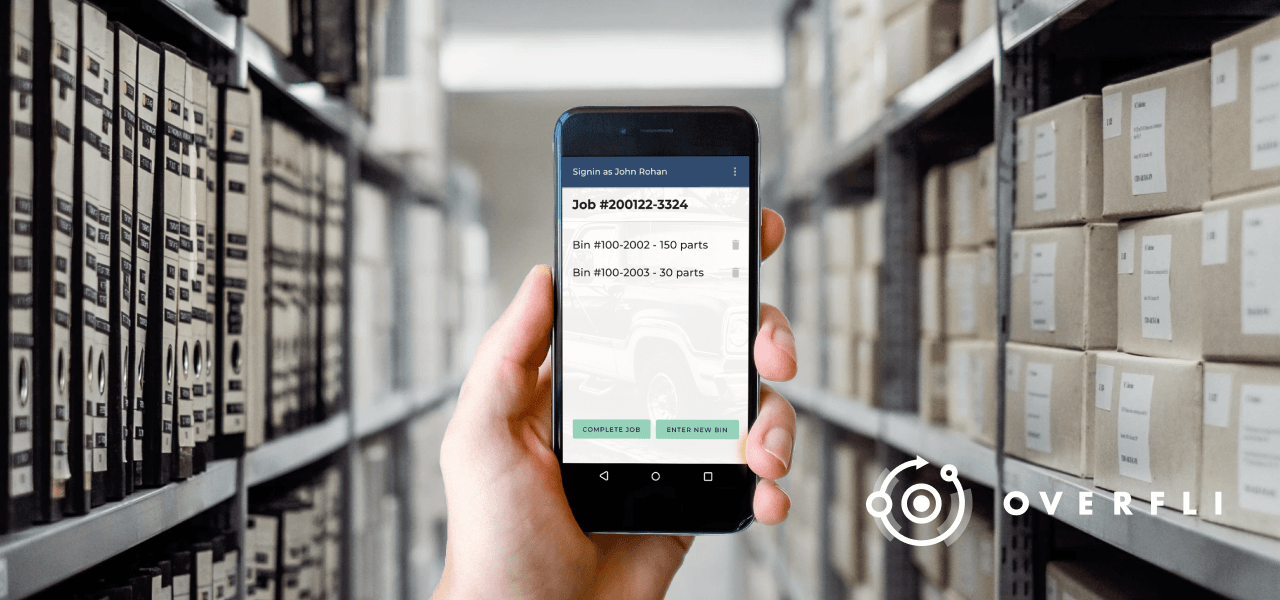
Overfli is a US company providing warehouse optimization services around the country. Their solutions help those struggling with labor-intensive and error-prone manual inventory processes, to avoid inaccurate accounting and frequent mix-ups.
They teamed up with Digiteum to build an Android app for warehouse optimization. This business-to-employee solution integrates with barcode scanners to automate stock verification and reporting. It functions online and offline, ensuring data integrity even with inconsistent Wi-Fi.
The admin version allows real-time inventory monitoring, quick adjustments, and workflow optimization.
Benefits
- Informed decisions.Real-time data lets managers make quick, informed decisions from anywhere.
- Streamlined operations.Mobile tech and ERP/WMS integration enhance efficiency and smooth out supply chain processes.
- Accurate and reliable data.Automated updates and real-time monitoring boost accuracy and reduce errors, even with spotty Wi-Fi.
Digiteum's decade-long tech expertise at your service
We solve key logistics and supply chain issues with smart automation. Discover how to optimize warehouse space, cut costs, and boost efficiency.
Check our servicesWarehouses are feeling the crunch as demand and product lines expand. Warehouse storage optimization is becoming a major challenge. With high real estate costs, everyone is looking into using warehouse space optimization techniques rather than relocating.
The game-changer?
Automation.
Warehouse optimization solutions like automated storage and retrieval systems (AS/RS) and shuttle systems make the most of your vertical space, reducing the overall storage footprint. Advanced WMS modules also simplify how you store and pick inventory, making sure you use every bit of space effectively. Overall, these solutions streamline space usage, speed up picking, and cut down on labor costs.
Real-life example: Hamilton Beach makes better use of space in its distribution center with new racking
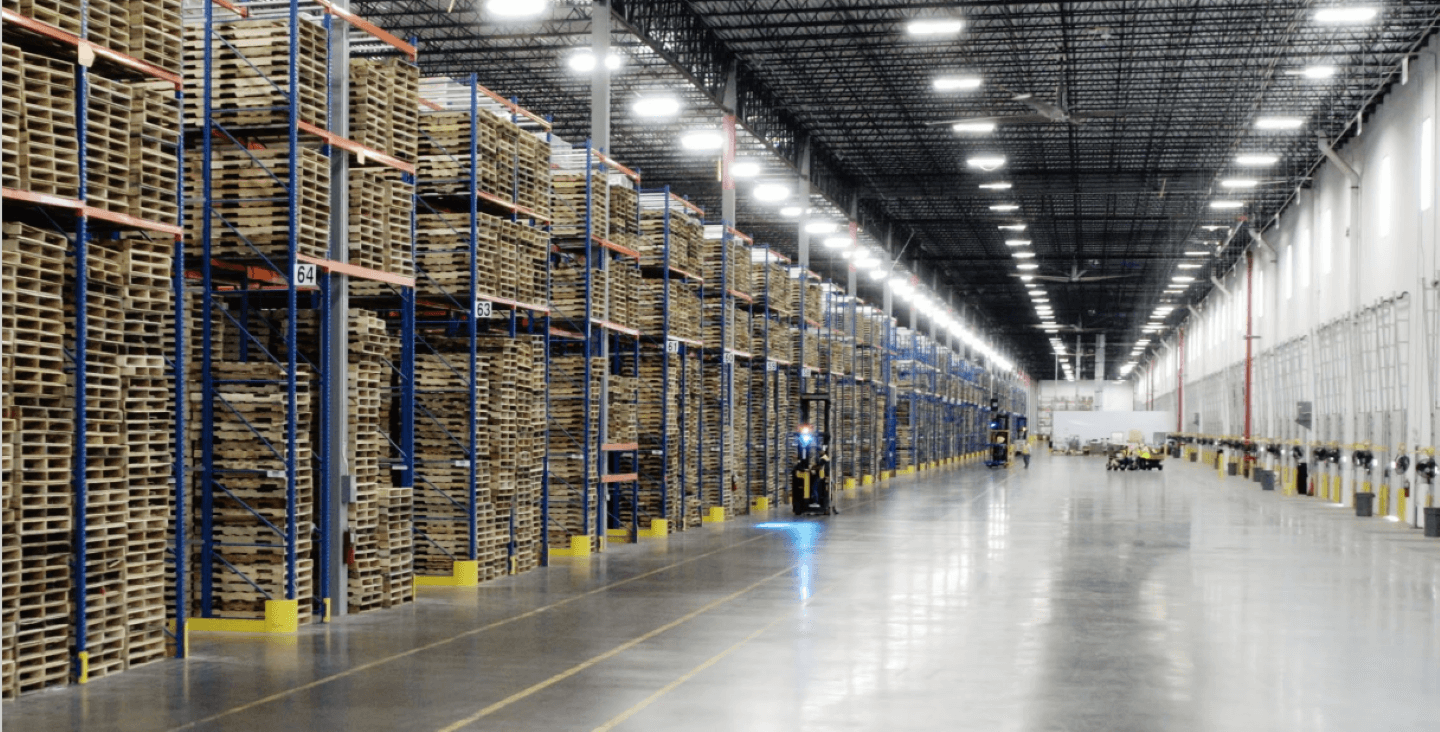
Image credit: Yale
Hamilton Beach, known for its kitchen appliances, moved to a new distribution center in Byhalia, Mississippi. The old warehouse struggled with disorganization, product damage, and limited capacity.
To fix these issues, Hamilton Beach revamped its facility with new racking. The shift from floor-level storage to multi-level racks included better use of vertical space, narrower aisles, and 80% double-deep storage. The racking was designed to work seamlessly with the new electric lift trucks, equipped with cameras and real-time monitoring solutions.
The new setup paid off big time: they doubled their eCommerce output, cut product damage by 80%, and slashed utility costs by 75%. The facility also maintained a top safety record with zero security incidents in the first eight months.
Benefits
- Maximized space utilization. Automation systems like AS/RS optimize vertical space, cutting the need for extra real estate.
- Faster operations. Automated processes speed up inventory handling and order fulfillment.
- Lower costs. Automation reduces manual labor and utility expenses.
Order picking in warehouses eats up to 50% of labor. The main issues? Reading labels, entering data, and too much walking. These inefficiencies waste time, hike up costs, and slow things down.
In a busy warehouse, this can be frustrating. Workers deal with delays, errors, and rising costs. Managers need a better solution.
Voice-directed technology could be the answer. It uses voice commands to guide workers, cutting out manual data entry and reducing mistakes. This hands-free approach makes picking faster and more accurate while saving on extra inspections and packing work.
Voice-picking systems typically synchronize with Warehouse Management Systems (WMS) or Enterprise Resource Planning (ERP) software for seamless data exchange and faster operations across a whole warehouse.
Real-life example: Würth Austria increases picking performance and cuts errors with a voice-directed system
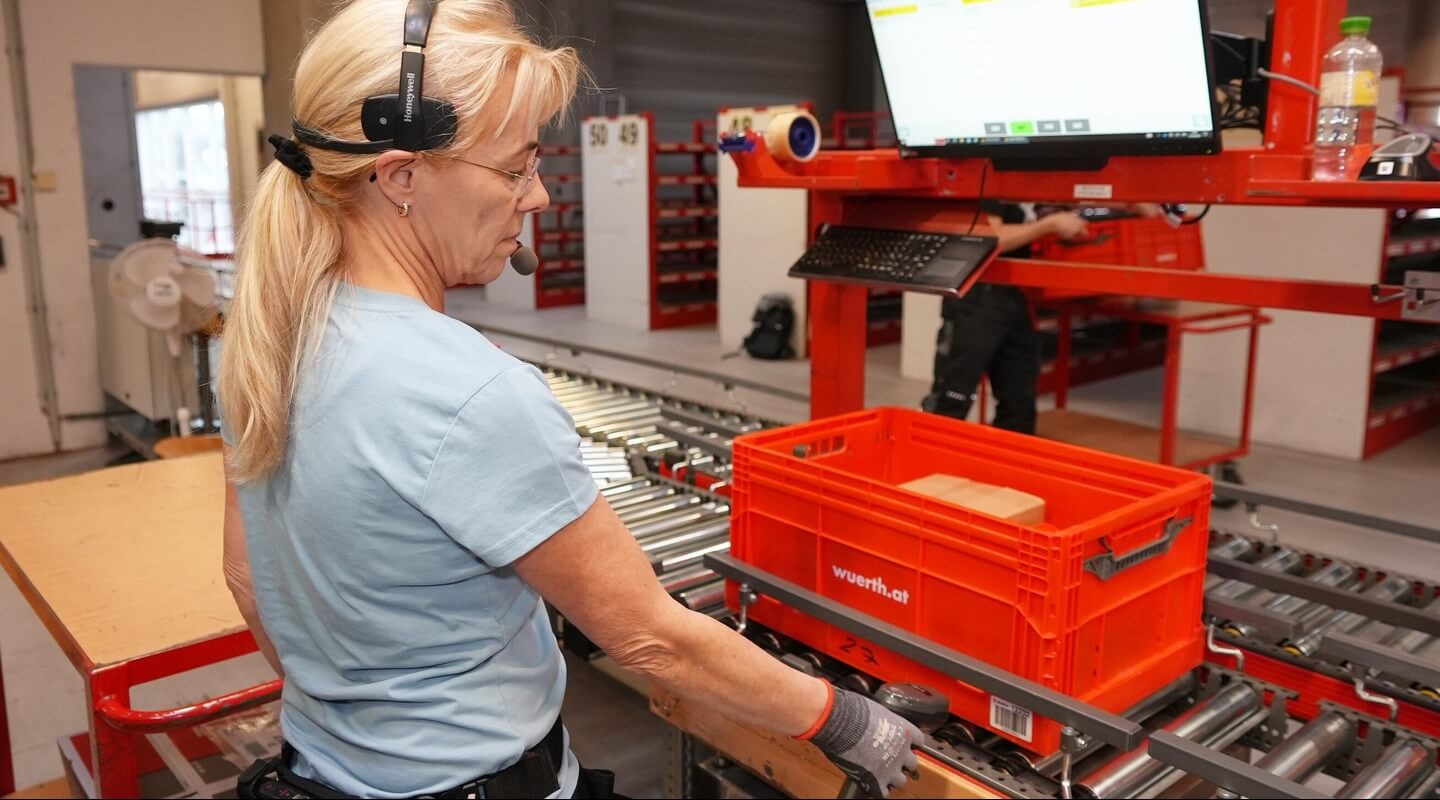
Image credit: Honeywell
Würth Austria, a key player in assembly and fastening materials, had trouble with an old paper-based picking system in their 1,200 m² warehouse. The outdated method led to waste and inaccuracies.
To fix this, Würth Austria teamed up with a technical service provider to implement a SaaS-based voice-directed picking system. The warehouse optimization solution includes wireless headsets and mobile devices, which work seamlessly with their ERP. This new system replaced the paper lists and guided pickers with voice commands.
The results were impressive. The solution improved picking performance by 15%, reduced errors from 3 to 2 per thousand picks, and cut paper usage by about 500,000 sheets annually. The new system has already boosted operational efficiency and is set to pay off within three years.
Benefits
- Reduced labor costs. Voice-directed technology cuts labor by minimizing manual tasks and data entry.
- Increased accuracy. Hands-free voice commands reduce errors in order picking and inspections.
- Faster operations. Synchronization with WMS or ERP speeds up warehouse processes and enhances efficiency.
Since 2010, Digiteum has been working on software development and warehouse optimization solutions for SMEs and corporations in warehousing and supply chain management.
- Boosting operations across the supply chain. We optimize warehouse operations, marine transport, and manufacturing with our automation services.
- Trusted partnerships. We work with clients like US-based Overfli to build warehouse products and help Swiss company Rollomatic develop custom in-house solutions.
- Smooth data integration. Our expertise in big data development services guarantees that your systems work together seamlessly, keeping your data flowing effortlessly.
Let’s team up!
With our skilled team, tried-and-true methods, and a flexible approach, we’ll create a solution that automates your warehouse operations and takes your business to new heights.
Hire logistics expertsIn their recent report about supply chain maturity, Accenture identified the four main stages:
- Past. Legacy tech, manual tasks, limited data.
- Now. Basic digital tools, partial automation.
- Near. Full digitization, high-quality data, eco-friendly practices.
- Next. AI and machine learning for autonomous decisions and continuous improvement.
Today, 80% of companies are at the “Past” or “Now” stages and plan to reach the “Near” stage in two years.
What does this mean for you? The industry is still adopting new tech. You’re not alone if you feel behind. To stay competitive, start integrating new warehouse optimization techniques now. Digiteum can help you implement automation and smart systems efficiently.